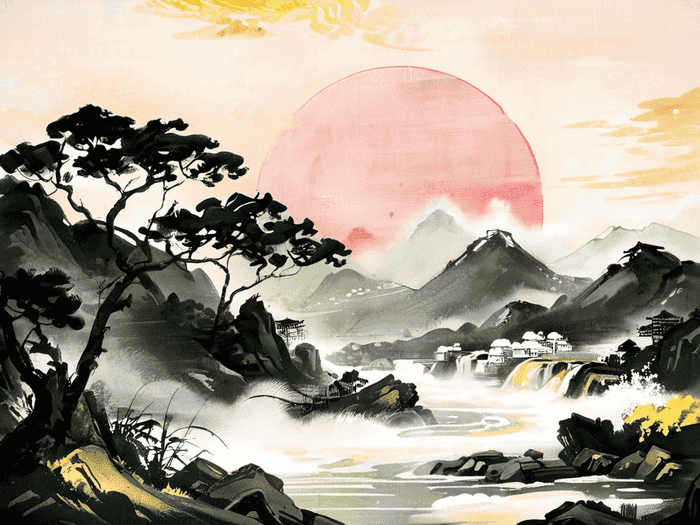
花开花落为您分享以下优质知识
设备与产能的计算需要综合考虑多个因素,以下是详细的计算方法和注意事项:
一、基础计算公式
产能的基本计算公式为:
$$
text{产能} = text{设备数量} times text{单台设备产能} times text{设备利用率} times text{设备效率}
$$
其中:
生产线上或工厂中拥有的设备总数;
每台设备在单位时间内能生产的产品数量(如每小时产量);
实际运行时间与计划运行时间的比率(通常以百分比表示);
实际生产数量与理论生产数量的比值(通常以百分比表示)。
二、分步计算方法
基于设备设计参数计算,例如:
$$
text{理论产能} = text{设备数量} times text{单台设备小时产能}
$$
其中单台设备小时产能 = 每小时产量 × 每天工作小时数(如24小时)。
实际产能计算
考虑实际运行因素:
$$
text{实际产能} = text{理论产能} times text{设备利用率} times text{设备效率}
$$
需通过历史数据统计得出设备利用率和效率。
三、其他关键因素
工作时间与班次
需明确设备每日实际运行小时数,扣除计划停机、故障及非增值时间(如换模、清洁)。
综合产能调整
包含机械效率、产品合格率、人工因素(如休息时间)等:
$$
text{综合产能} = text{实际产能} times text{机械效率} times text{合格率} div text{人员效率系数}
$$
其中人员效率系数需根据实际用工情况调整。
四、示例计算
某工厂有10台设备,每台设备每小时生产10个产品,设备利用率80%,效率90%:
$$
text{日产能} = 10 times 10 times 0.8 times 0.9 = 720 text{个产品}
$$
五、注意事项
行业差异:
不同行业对产能计算标准不同,需结合行业规范;
建议定期(如月度)重新评估设备状态和效率,避免长期使用导致的性能下降;
使用OEE(综合设备效率)模型可更精准反映实际产能。
通过以上方法,可系统评估设备产能,并为生产计划和资源优化提供数据支持。